Making Conscious Choice for Planet Health
Regenerative Design
Regenerative practice is a way of living and functioning that is inspired by the natural world. It can be applicable to all aspects of our lives, from the way we cultivate our food to the product design process. As a Regenerative designer, I am committed to a holistic approach towards creating products and enhancing ecosystems to have a positive impact on the environment. Restoring traditional techniques and natural materials to create sustainable products, and prefer to use natural material for my creation. Perhaps, Natural & Vegetable dyes are my first choice to develop fabrics or garments. Natural dyes are antitoxic than synthetic dyes. Mostly, cotton fabric is used for natural dye printing, it provides solace during summer season. Apart from encouraging my clients to consider regenerative fashion, I have a penchant for dresses made from natural dyes and fabric. Shomaa Designs has collaborated with natural dye producers to develop new and innovative ideas to use Bagru Prints. Nowadays, the majority of Regenerative colorists pigment natural dyes like indigo, madder root, chestnuts, shibori, and weld.
The Decline of Natural Dyes During Industrial Revolution After Invention of Synthetic Dyes
The industrial revolution in the 18th and 19th centuries prompted significant changes in the textile industry, including the invention of synthetic dyes. An English chemist named William Henry Perkin in 1856 discovered the first synthetic dye. At the age of 18, Perkin was attempting to synthesize quinine, a medication used to treat malaria, from coal tar as part of his research. However, instead of obtaining quinine, Perkin accidentally discovered a purple dye, which he named mauveine. Perkin’s discovery of mauveine marked the birth of the synthetic dye industry, with renewed wonder a dye had been created through chemical synthesis rather than being extracted from natural sources. Mauveine was commercially produced and quickly gained popularity as a vibrant and stable dye that could be used to color textiles, clothing, and other materials. This breakthrough paved the way for the development of many other synthetic dyes, leading to the growth of the modern chemical and textile industries. The invention of synthetic dyes revolutionized the textile industry, as it allowed for a wide range of colors to be produced in a more consistent and affordable manner compared to natural dyes. Synthetic dyes quickly replaced natural dyes in many textile applications due to their versatility, stability, and cost-effectiveness.
The widely and commercially used synthetic dyes impart strong colors but cause carcinogenicity and inhibition of benthic photosynthesis (Adeel, 2009). The
synthetic dyes had some advantages over natural dyes like color fastness, good reproducibility of shades, brilliance of colors and easy to use. These synthetic dyes produced hazardous by-products, some of which carcinogenic intermediates and hence a ban has been imposed by Germany and European countries on the use of benzidine dyes in textile garments exported into their countries. (M.C.Purhoit, 2012, Volume2, Issue 2). Synthetic dyes are made from petroleum-based products, and they can contain harmful chemicals. They require a lot of energy and water to produce, and they can pollute waterways when they are released into the environment.
However, concerns about the environmental impact and health effects of synthetic dyes have led to a renewed interest in natural dyes in recent years, and the use of both synthetic and natural dyes continues to coexist in the textile industry today.
Revival of Natural Dyes In 21st Century
One of the main drivers of the revival of natural dyes is their skin-friendly and sustainable nature. Natural dyes are typically produced using less energy and water, and they are biodegradable. Furthermore, natural dyes are often perceived as safer and healthier compared to synthetic dyes, as they do not contain harmful chemicals such as heavy metals or carcinogenic compounds. This makes natural dyes a popular choice for those who are concerned about the potential health risks associated with synthetic dyes, including artisans, craftspeople, and consumers. The effluent contains hazardous chemicals which cause, among other things, skin diseases and lung problems.
The word “natural dye” covers all the dyes derived from the natural sources like roots, stems, barks, leaves, fruits and seeds may contain coloring matter which can be extracted through different methods. India is one of the 12 rich mega Biodiversity countries in the world and includes in 8 major centers for origin and diversification of study of vegetation (M.C.Purhoit, 2012, Volume2, Issue 2). Some natural dyes also contain natural mordents. Mordents are metal salts which produce an affinity between fabric and dye. Many natural dyes are produced by small-scale farmers and artisans in developing countries. These craftsmen are involved from earlier generations and continue to practice their traditional craft. By using these natural dyes, regenerative designers can support these communities and help preserve traditional dyeing practices. That’s why Natural & Vegetable dyes are the first choice of regenerative designers.
Let’s deep dive into history of Natural & Vegetable Dyes
India’s expertise in natural dyes dates back to ancient times, with even the Vedas referring to their properties. India has a centuries old tradition of usage of natural dyes for dyeing and printing application. The colors and coloured forms are used in different forms in prehistory. Fragments of cotton textiles dyed by complex processes are dated back approximately 2000 B.C. The excavations of Mohanjo Daro in the Indus valley of India (J.N.Liles, 1930) have revealed plenty of such proofs. Eventually dyeing using natural pigments got developed as folk art. In India, Rajasthan and Kutch (Gujarat) still possess a rich tradition in the use of natural dyeing. Rajasthan state holds a unique position in natural dyeing and printing. The art of producing natural dyes on textiles is being practiced in many villages by dyers and printers in Rajasthan. Pipad in Jodhpur district of Rajasthan is famous for natural dyes works on cotton fabric using block printing method. Rajasthan Saganer, Bagru, Barmer, Jodhpur, Akola( Chittorgarh district) have been famous centers for dyeing and printing using natural mineral based dyestuff.
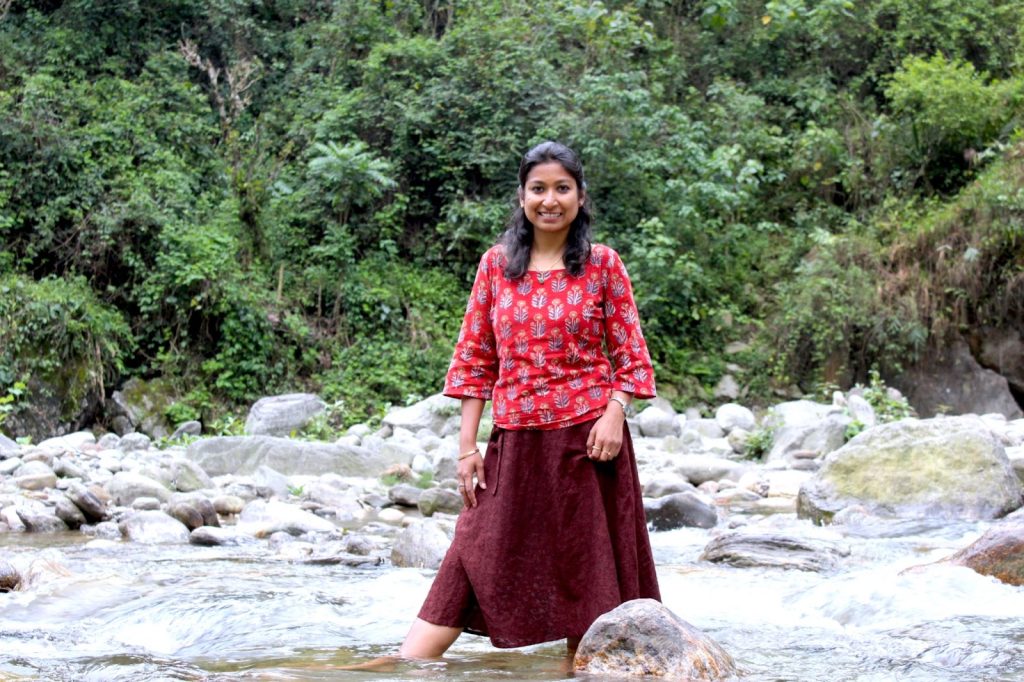
Bagru is most famous for its typical wooden hand block prints. Bagru is a town and a municipality in Jaipur district (Tehsil Sanganer) in the state of Rajasthan, India. It is located at a distance of 32 km from Jaipur, on Jaipur-Ajmer Road. Bagru is the home of both the Raiger and the Chhipa community, or traditional craftspeople who printed textile articles by hand, using natural dyeing and indigo dyeing colors. These prints of Bagru are widely acclaimed, and known as “Bagru prints”. Bagru Chhipa came from Sawai Madhopur, Alwar, Jhunjhuna, and Sikkar districts of Rajasthan to settle in Bagru and make it their home around 450 years ago. Chhipas have been involved in the fabric printing tradition for over 100 years. In Chippa Mohalla (Printer’s quarter) one can walk into the quarter, where people are always engrossed with dyes and blocks. The three-centuries-old tradition of block printing is kept alive with the efforts of Bagru artisans.
All the motifs are first carved on wooden blocks which are made by craftsmen called KHARAUDI. They specialize exclusively in the skill of hand-carving the designs on the blocks and do not use the electric machinery. They work with their traditional tools which include a ruler, compass, saw and wooden maller.
Usually Bagru prints have ethnic floral, spiral, geometrical and figures like fishes etc.patterns in natural colors. Main patterns carved on the blocks are:
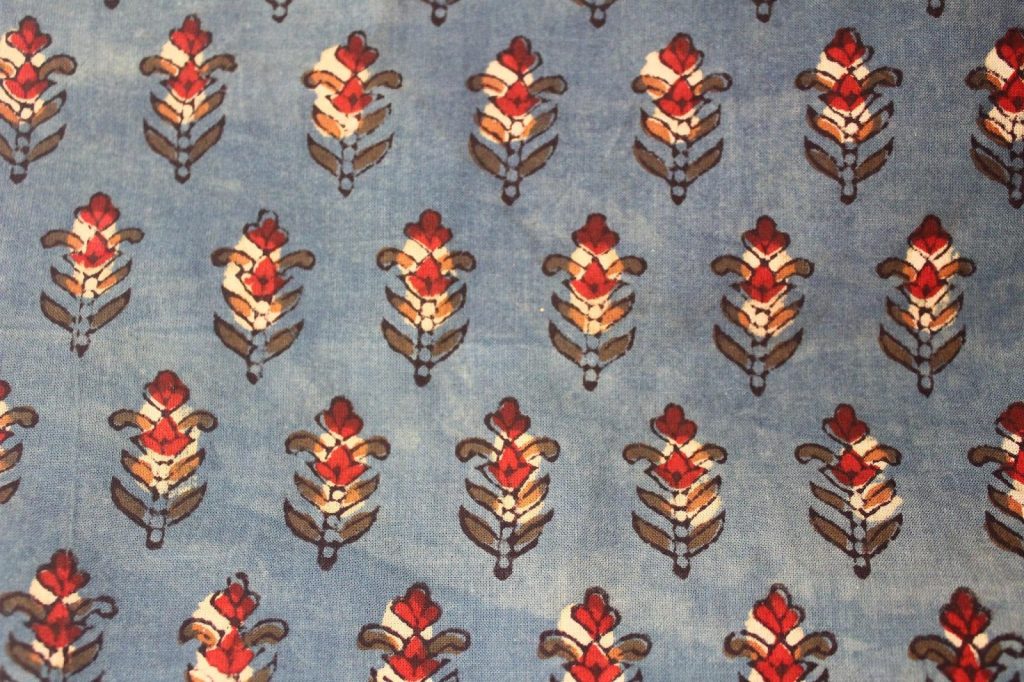
1) PATASHI with its tiny floral designs of buds, leaves and stems.
2) JHAD with its interviewing tendrils and distinctive border lines.
3) HATHI- the elephant
Bagru prints form the essential part of the block printing industry of Rajasthan. The village fabricates some of the bed covers and other materials. They are known for their unique designs of luxuriant trellises in sophisticated natural colors. Printed Lengths of rough cotton about 50 cm wide were typically sewn color, and different prints served as identifying emblems for various Hindu castes.
Pipad, a small town in Jodhpur district of western Rajasthan (65 km from jodhpur city) is producing good hand block prints. Dry arid climatic conditions at Pipad are favorable for hand block prints. The conventional art of printing using natural dyes colors on cotton fabric by wooden block is the speciality of this place. The motif and color is inspired by local traditions, flora and fauna of this area. In the 80’s more printers practiced this craft but due to decline of demand of natural fabrics and availability of widely available and cheaper synthetic printed fabrics, most dyers and printers left this craft in the era of 1980-85. Here “Yaseen Shahabuddin and his family” has been continuously doing this work from the last five to six generations. Presently they are using natural dyes for cotton, cotton silk and silk printing and sell the fabric to buyers like FabIndia, Rangotri and other national andinternational markets. The most common raw materials used by craftsmen at Pipad village were harada (myrobolan), Iron fillings, Gud (jaggery) , Alum, Kesula flowers, Natural Indigo, Guar gum or Babool gum ( thickener).
Printing Process:
The process begins with the plain cloth. The raw fabric usually contains different kinds of impurities like oil and dust, starch which needs to be cleaned to remove these impurities. The Chippa community requires two days to prepare a paste by mixing soda ash, sesame oil and cow-dung and washing the cloth with this mixture. This cloth is now washed, dried and ready for the “Harda” treatment. In these treatments the fabrics are then squeezed to dry and laid down in the sun. Almost each and every stage requires the cloth to be washed in water and dried in the sun to remove the impurities. Nowadays, the village community has made a new initiative to reuse the used water for recycling or charging inside the ground.
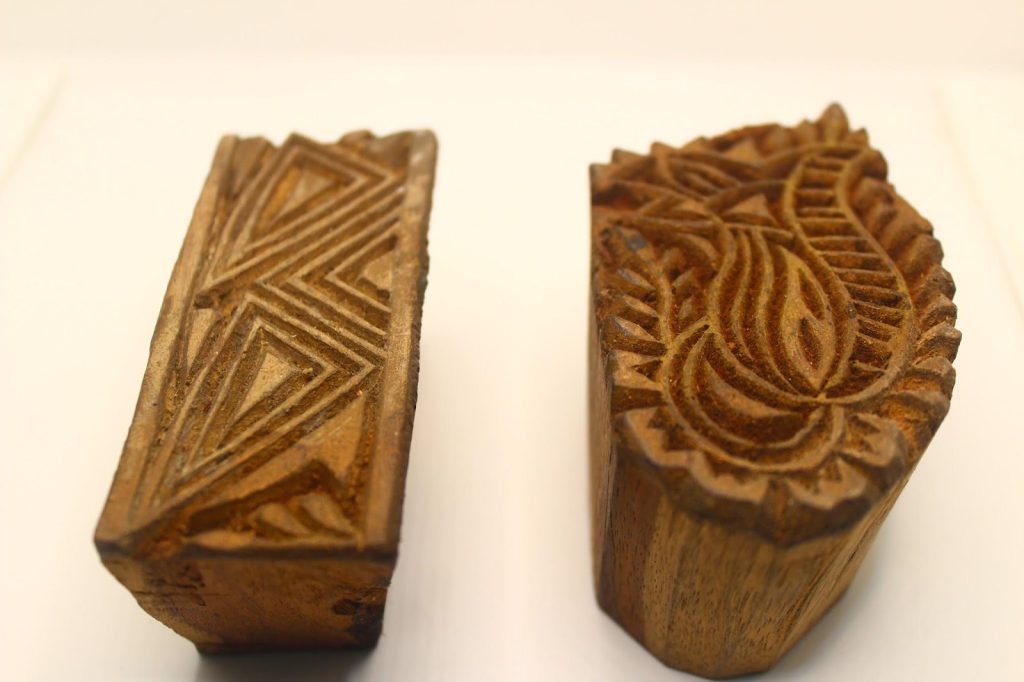
Blocks made of wooden for hand block prints
The unique method for printing employs wooden blocks in it. In the process, the desired design is engraved on the wooden block first and then the carved block is used for replicating the design in the preferred color on the fabric. Keeping the convention, these artisans smear the cloth with Fuller’s earth from the riverside and then dip it in turmeric water to get the habitual cream color background. After that, they stamp the cloth with designs using natural dyes of earthly shades. Even today, artisans use traditional vegetable dyes for printing the cloth. Like, the color blue is made from indigo, greens out of indigo mixed with pomegranate, red from madder root and yellow from turmeric.
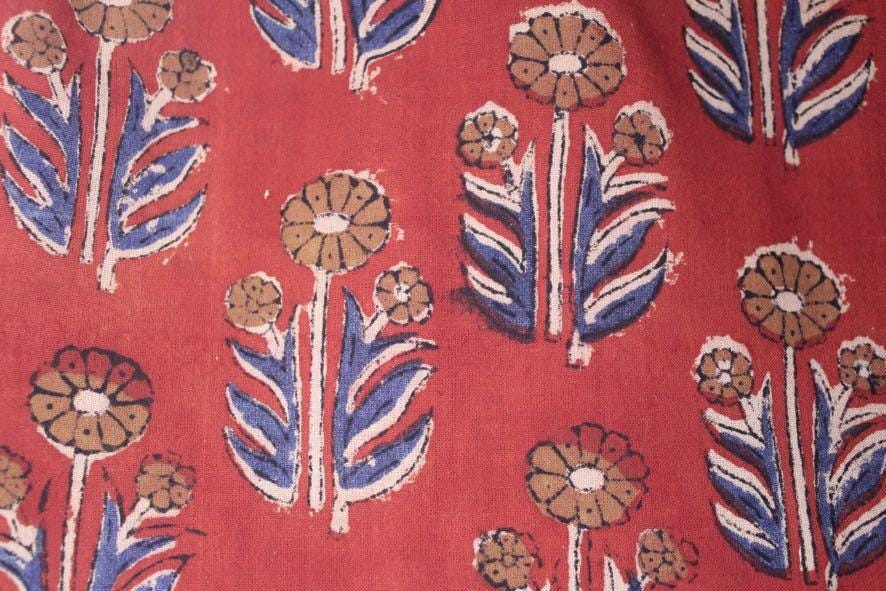
NATURAL RED: At the very first, a gum paste solution is paste in water and then strain through a cotton cloth. When the color is applied on the fabric it appears brown in color with the help of the blocks but after the fabric is placed in the furnace the color turns into red.
Two types of printing process are used:
Direct Dye Printing – In the very first process,the dye solutions need to be poured in the tray. The printer presses the block into the dye tray.The outline pattern is done in blocks for the background and highlights in different colors. Once each of the patterns is complete, the cloth is ready for the dye vat. This printing is mainly done by male printers.
Resisting Printing – A different type of printing Technique of resist style called “DABU” printing, which is primarily known for its mastery design. Its quintessence remains in printing with specially prepared “Dabu” paste, then they apply the thick black mud paste on the cloth and then dye the fabric. Each family follows its own trick to create a distinctive Dabu paste.
In both of the procedures, firstly the blocks are soaked with refined oil or mustard oil overnight and then washed. Wooden tables are mainly used for this printing, the size of the cloth of which depends on the length of to be printed.
Future of Natural Dyes in Regenerative Fashion
Natural Dyes are the future of regenerative fashion. Because they are biodegradable, meaning that they can be broken down by microorganisms and returned to the environment at the end of their life cycle. Natural Dyes can be produced using regenerative agriculture practices, which help to improve soil health, reduce water pollution and increase biodiversity. The regenerative design movement is still in its early stages, but it has the potential to transform the way we design and construct our world. By creating systems and solutions that are regenerative, we can create a more sustainable and equitable future for all.